
Les Thorne
A production spindle turner who’s been on the registry of professional turners since 2001
The last time Les visited Chelmer Valley Woodturners was about two years ago. This time, he a full hall of members to where he explained his process of making a bowl. Les told us he doesn’t make many bowls, so enjoys doing them at demonstrations, he said that only makes 150(!) per year. The evening was full of anecdotes and idioms which brought the evening to life.
Firstly, he ran through the use of a bowl gouge and its uses compared to a spindle roughing gouge, interacting with members as getting their view, which was something Les returned to through the evening.
Moving onto the wood, he mentioned his approached to turning a bowl. ‘A curve is made with an infinite amount of straight cuts’; Les used five to start the simple curve he was going for. After this, he demonstrated his continuous bead for the decoration. This was a new technique to most at the club and something that was very impressive to behold!
All the beads were created in successively, in one cut, from bottom to top.
Les then shared his thoughts about colours on wood. He said that natural woods sell well, with spalted woods, yew and natural edge objects being a public favourite.
‘Everyone has a bit of stain in their cupboard, why not use it?’ Les mentioned one of his students used fence paint on a project and it turned out well!
One technique Les returned to frequently, was the difference between pull and push cuts and describing them in two general forms.
A push cut has bevel support and therefore the tool rest positions is not as important as a pull cut. A push is where the tool is moving in front of the cutting edge.
A pull cut does not have bevel support, therefore the tool rest ideally needs to be as close to the piece as possible. A pull cut is where the tool is moving behind the cutting edge (therefore it’s not a great idea to pull but inside of a bowl).
Les’ words of wisdom
Risk assess every time you approach the lathe
In the shed, use full face protection.
In general, people don’t take off enough wood to make a good curve
Speed is our friend - Until the wood comes off!
If your thumb goes white, you’re holding the tool too hard.
Stop approaching the wood as if you’re going to kill it!
A gouge wants to cut in the direction of it’s bevel
Brown and Black work well together to create interest
Power sand at 3 o’clock (in a bowl), hand sand between 6 and 9
A small tool means a small cut - Use the tool appropriately
Les prefer a thick rim and a thin base, as he feels it sits better
‘If you’re going to bugger up a project, bugger it up at the beginning’

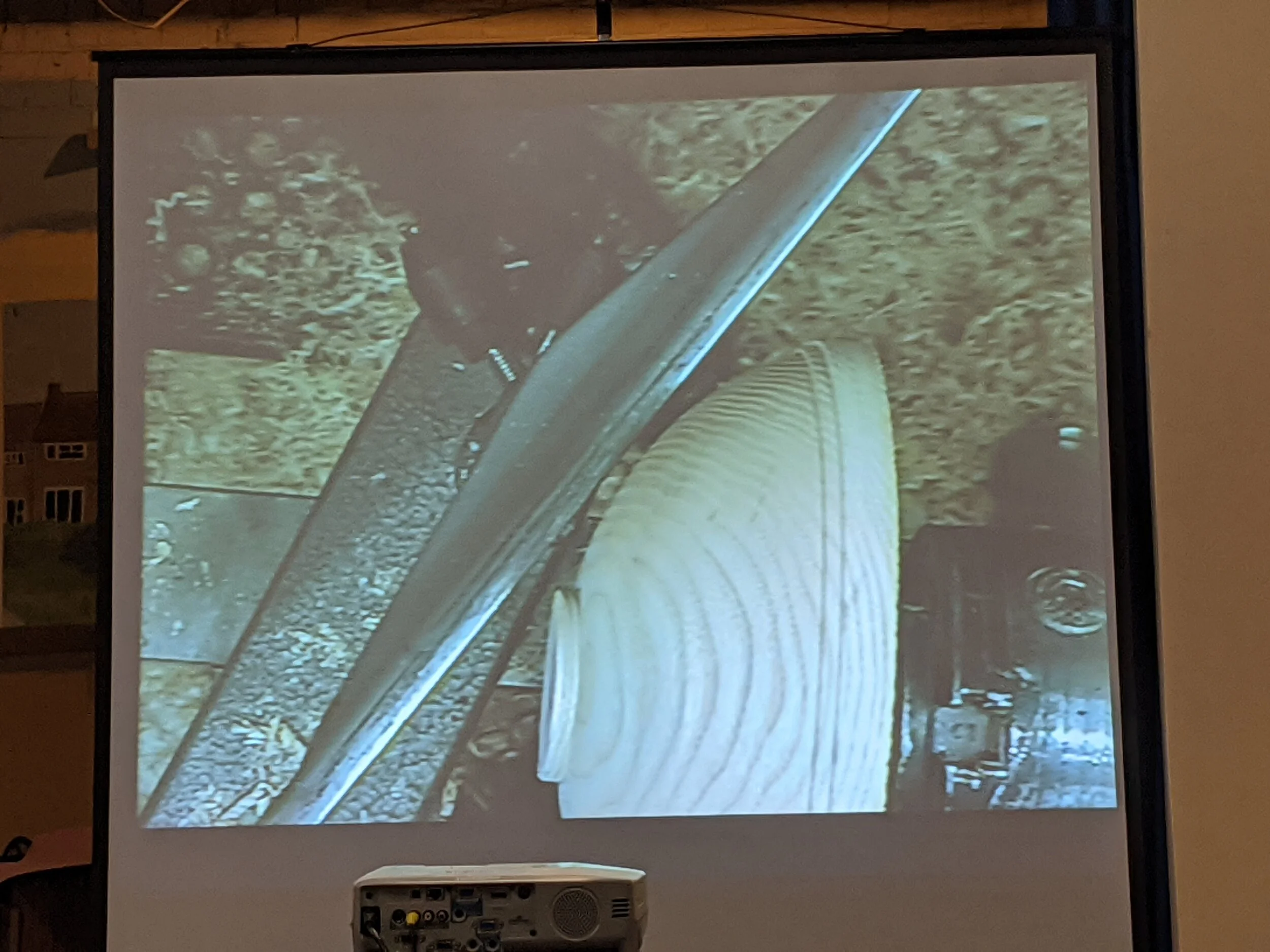



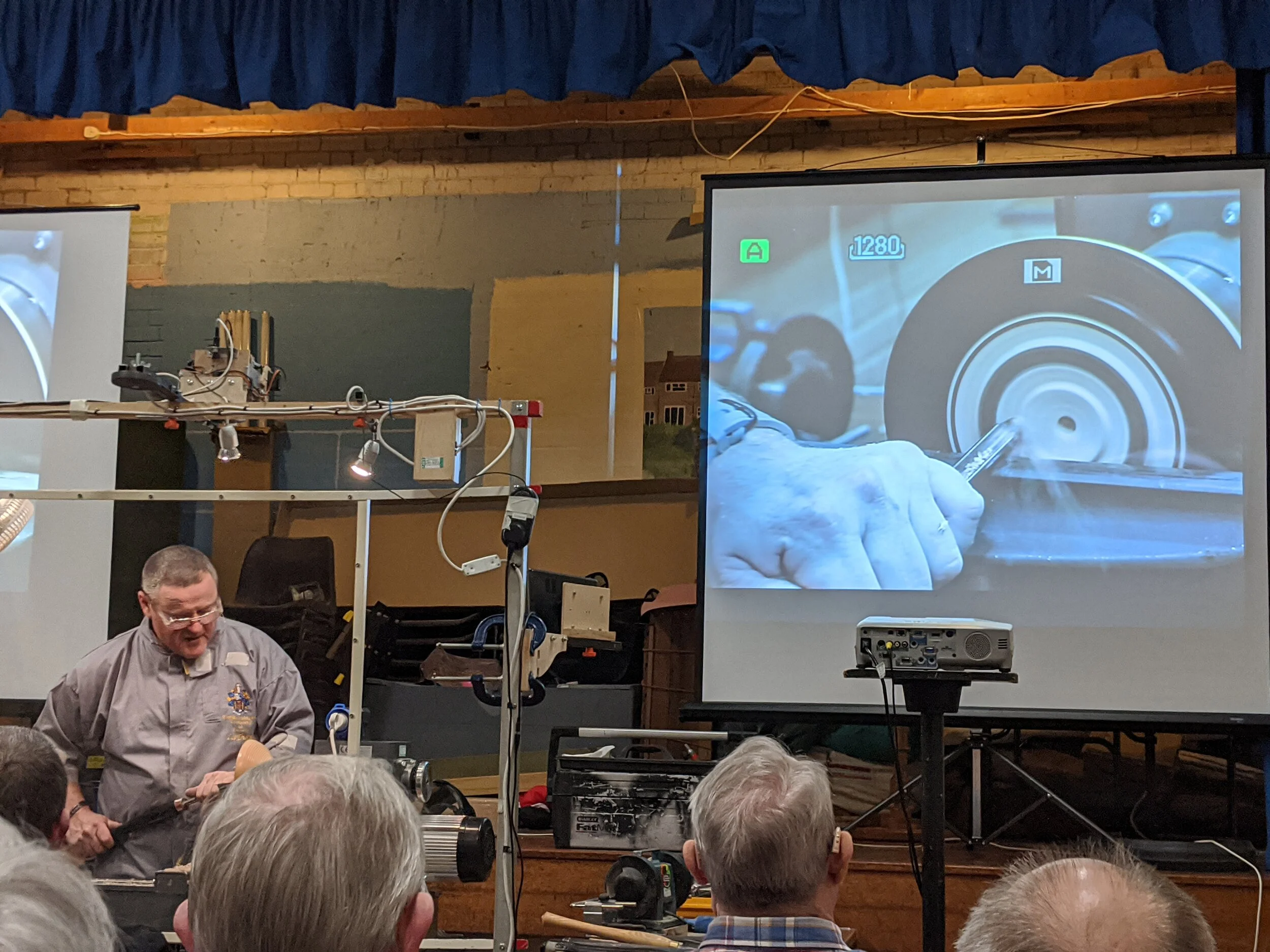




